AN AUTOMOTIVE EXPANSION
First stage began March 2021 and ended with the expansion in February 2022
PROJECT INFORMATION
To keep pace with the expansion, Prodensa helped the client acquire a small warehouse within the same industrial park. This allowed the client to meet production demands. By February 2022 the complex expansion was completed.
EARTHWORKS
- Acquisition of 29,988.11 m2 of land for the expansion
- Process drainage system consisting of 4-4m2 independent systems
- Storm water channel and city water distribution
STRUCTURAL
The expansion consisted of 22,081.37 m2 of standard metal-roofed construction with precast walls and insulated metal sheet roofing.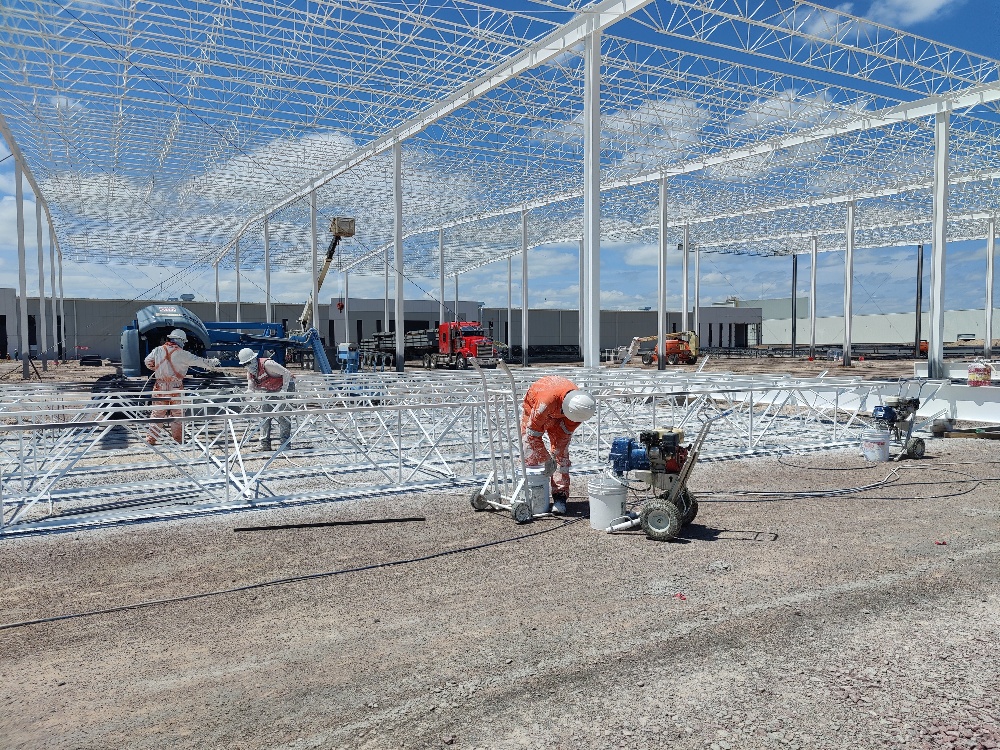
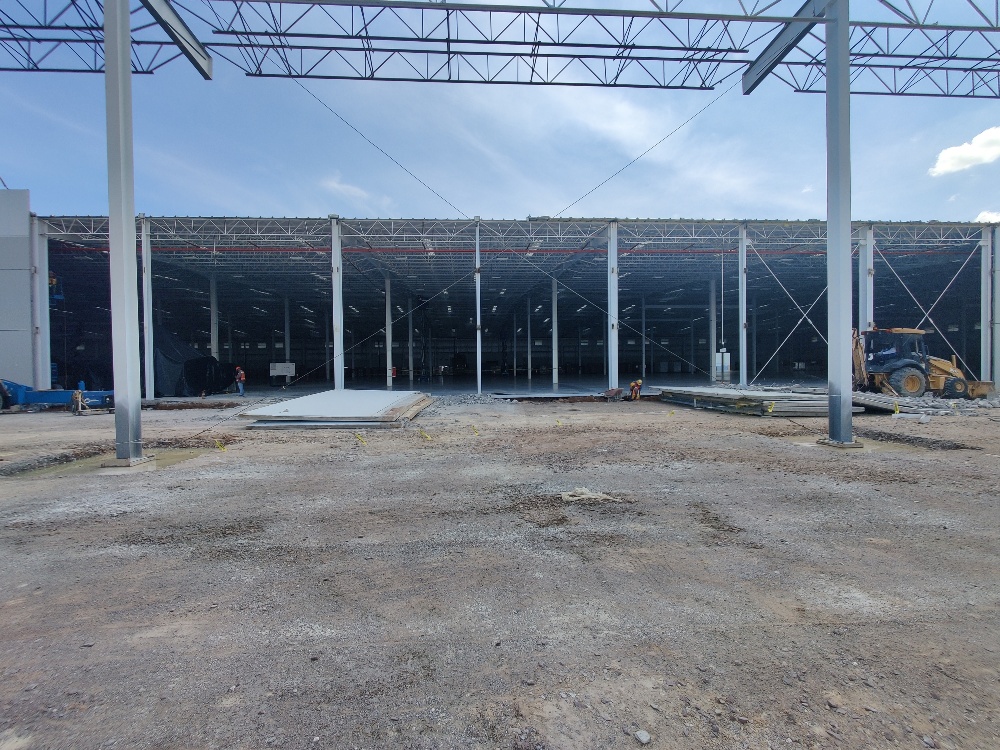
Axis A wall removal and preparation for expansion connection.
ELECTRO-MECHANICAL SYSTEMS
Within the scope included the preparation of:
- A specialized painting process
- A compressed air system
- A water chiller system
- Water cooling towers
- Dust collection system
- WIP paint finishing room
- Moisture control room
- Natural gas distribution loop with 4" pipe
- Electrical system
- Reverse osmosis water treatment system
- Specialized flooring for plastic injection molding machines
THE EXPANSION
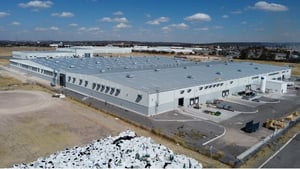
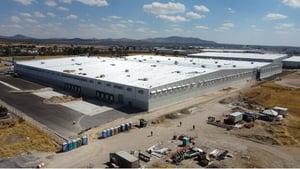
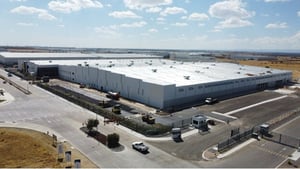
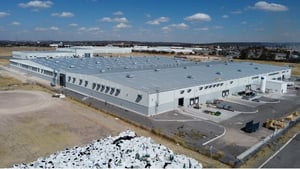
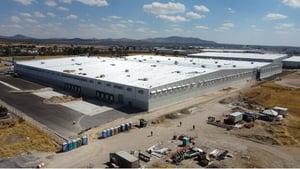
CHALLENGES
One of the most significant challenges in the building expansion was the removal of existing precast concrete walls to physically and operationally merge two separate buildings into a single, cohesive production facility. This process presented several technical, logistical, and safety-related obstacles that needed to be addressed to ensure a seamless transition and minimal disruption to operations.
-
Structural Integrity & Engineering: Removing load-bearing precast walls required engineering assessments and temporary supports to maintain stability and prevent damage.
-
Operational Continuity: Phased demolition was necessary to keep production running, with work scheduled during off-peak hours and dust control measures in place.
-
Demolition Logistics: Specialized equipment, including cranes and cutting tools, was needed for safe removal, along with proper waste management and recycling compliance.
-
Building System Integration: Electrical, HVAC, fire suppression, and drainage systems had to be merged, requiring adaptive engineering solutions for seamless functionality.
-
Regulatory Compliance: Permits, safety regulations, and coordination with authorities were essential to prevent delays and ensure legal adherence.