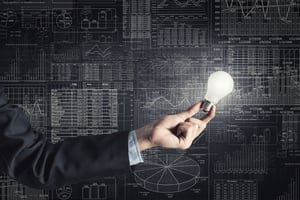
CRISIS MANAGEMENT IN AUTOMOTIVE MANUFACTURING
This case study demonstrates PRODENSA's expertise in crisis management and production efficiency optimization within the automotive industry. By providing a tailored, industry-specific solution, PRODENSA not only resolved the immediate crisis but also established a framework for continuous improvement.
PROJECT OVERVIEW
The client, a major player in the Electric Vehicle (EV) industry based in the United States, faced significant production delays at one of their key supplier factories in Mexico. With overall production efficiency not reaching 50%, the client sought a solution to address these inefficiencies and ensure timely delivery of critical components. PRODENSA was engaged to design and execute an effective production plan that would reduce delays, eliminate errors and reworks, and increase the rate of production per unit of time.
PROJECT STAGES
CHALLENGES
- Stringent Quality Standards: The automotive industry’s high standards made it essential to maintain consistent quality during the crisis, which was challenging under tight timelines.
- Complex Supply Chain: The intricate nature of the automotive supply chain added complexity to identifying and addressing issues within the network.
- Regulatory Compliance: Ensuring compliance with industry, safety, and environmental regulations was critical, especially during the crisis.
- Production Downtime: Any disruptions in the manufacturing process had the potential to cause costly delays.
- Financial Impact: Balancing the need for immediate corrective actions with cost control was a significant challenge.
SOLUTIONS
Project Outcome
PRODENSA's intervention led to a significant turnaround in production efficiency, with overall efficiency increasing from below 50% to nearly 100%.
As a result of this successfully completed assignment, PRODENSA was introduced to the other business divisions of the CLIENT to support in further projects.
Key achievements included:
- Stopping the crisis from escalating further.
- Optimizing and balancing 11 assembly lines.
- Standardizing critical production processes, resulting in improved output quality.
- Reducing the need for 24/7 shift operations.
- Meeting higher customer expectations by increasing the rates of production per hour/day.